Industry 4.0: AI solution for manual workstations
At the beginning of the last decade, the manufacturing environment has undergone a major transformation: the so-called Fourth Industrial Revolution. It is characterized primarily by the sensing of workstations, machines, equipment and industrial devices and their connection to the Internet. This definition also explains the development of Industry 4.0.
See below the main characteristics of this new era of industry and the AI solutions that optimize industrial processes.
A transformation that is not yet for everyone
Before Industry 4.0, managers did not have access to all the information and metrics obtained in companies. Now, with digital transformation, it has become easier to make strategic decisions based on data.
However, this transformation is not yet for everyone. On production lines, there are manual workstations. In these places, obtaining the metrics and data that ensure the quality and credibility of the product is still very complex.
Here are some problems that manual workstations still have:
missing parts or components of the product;
defects resulting from incorrect assembly of the product;
products assembled with incorrect parts;
difficulty in managing product quality, usually done by sampling;
scrap or discard of products already assembled because they do not meet the quality standard;
reduced productivity;
difficulty and high cost to train new employees;
product defects perceived by the final consumer, which generates brand depreciation.
Artificial Intelligence: the solution to solve the problems of manual workstations
As you have seen, there are still many problems faced by industries that have production lines with manual workstations. To solve them, the most effective solution is to use artificial intelligence systems.
These systems allow quality control in repetitive manual assembly processes in real time and of all the units produced. Consequently, they eliminate the need to perform this control by sampling, a process that hinders the quality management of the products.
Macnica ATD Europe brought an artificial intelligence solution to Europe: the Retrocausal Pathfinder Apollo. This platform was developed by Retrocausal to optimize the control of manual workstations.
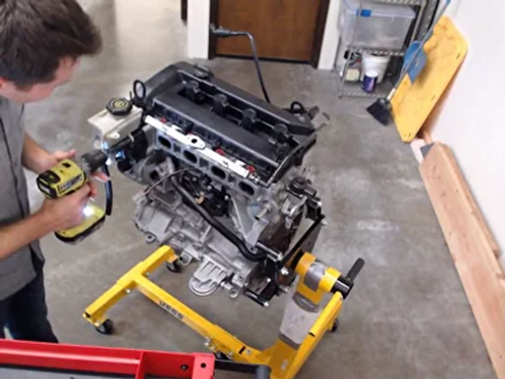
Get to know Retrocausal AI Solution
Retrocausal Pathfinder Apollo is a computer vision system that evaluates manual workstations automatically and in real-time. This AI solution is trained by monitoring the manual workstation. From this, it receives information about the sequence of steps the operator must take.
Once trained, this artificial intelligence system detects errors made by the operator during the assembly process. The error alerts are issued at the same time, preventing the defective product from advancing in the production line.
Thus, with the application of the artificial intelligence solution Retrocausal Pathfinder Apollo, the industry guarantees several benefits, such as:
up to 10% increase in the productivity of the manual workstation;
up to 60% reduction in the occurrence of quality problems caused by assembly failures.
In addition, the Retrocausal Pathfinder Apollo platform can be used for training new employees. This is possible because the sequence of steps is stored visually and descriptively.
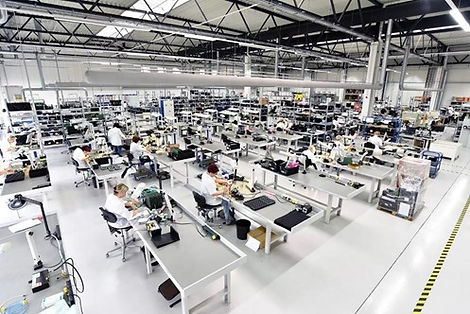
Here are some more monitoring tasks where the Apollo Pathfinder Apollo artificial intelligence solution can be applied:
total or partial assembly of motors and their accessories and peripherals;
assembly of product kits;
assembly of computers and other electrical and electronic equipment;
assembly of household appliances;
tool assembly;
assembly of miscellaneous items in plastic or metal.
Monitoring and metrics management can be done through Retrocausal's online platform. This platform allows integration with existing management systems.
Contact us for more information: marketing.mae@macnica.com