How to increase efficiency and reduce manual production errors?
Industrial automation within the concept of Industry 4.0 goes beyond the use of robots and automation of manufacturing processes. Thus, in order to continue increasing productivity, manual assembly must be improved, and this can be done with video monitoring.
In the industrial environment, where production steps are done by humans, the use of cameras and processing with Artificial Intelligence can be a great ally to increase productivity, and for that to happen, it is necessary to invest in:
Software: the intelligence embedded in the process must be able to process information quickly, send alerts in real time and generate insights to optimize the process.
Hardware: devices, such as computers, must be robust to process a large load of data, with thousands of frames per second coming from surveillance cameras; in addition, computers must be physically robust to operate in hostile environments such as factories.
People: there are manual assembly activities that only humans can perform, therefore, improve this process through solutions that monitor steps and issue visual and audible alerts in real time.
Knowing the importance of these pillars to increase factory productivity, Macnica ATD Europe has robust and efficient solutions in its portfolio to optimize manual and repetitive assembly, such as the Pathfinder Apollo.
For monitoring the video data collected, the Pathfinder Apollo is the ideal solution as it optimizes manual and repetitive assembly.
PathFinder provides real-time audible and visual alerts of missed steps, which prevents products from leaving the factory with assembly defects.
Installing the platform is quick and simple! With a camera, data is collected to train the artificial intelligence that will monitor the process. In addition, with just over 10 process samples it is already possible to have a trained system.
With the system configured, the platform monitors the process, showing the steps performed on the monitor and emitting audible alerts if any step is missed.
We know that even if operators work tirelessly and repetitively, inexperience, fatigue, new processes and production complexity can often lead to error.
Human errors can be responsible for 68% of quality problems on manufacturing assembly lines, can you imagine the gain in process efficiency offered by this solution?
Retrocausal's AI solution is able to monitor the entire process and trigger audible and visual alerts when an error occurs.
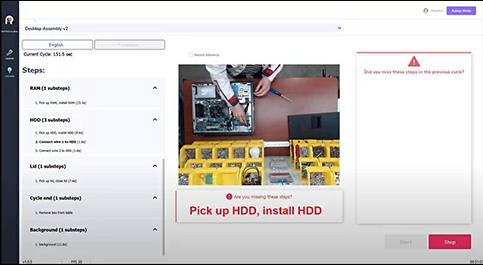
And people?
People, in addition to being fundamental in manual assembly, are not replaceable, but can receive great help from monitoring systems.
The PathFinder solution becomes an ally of the operator, ensuring that 100% of the products are correctly assembled. Can you imagine a better partner?
Another advantage of this system is that it can help new operators in the training process, showing which steps must be performed and signaling what has not been done correctly.
More benefits?
In addition to real-time alerts, the Pathfinder platform measures cycle times, step-level statistics, variances, and non-value-added activities.
This shows process variability and helps industrial and quality engineers to equalize manual production lines.
In other words, Pathfinder helps factories extract more productivity from their processes in the long term. All this is done by analyzing 100% of the production data, eliminating the concept of sampling and increasing reliability.
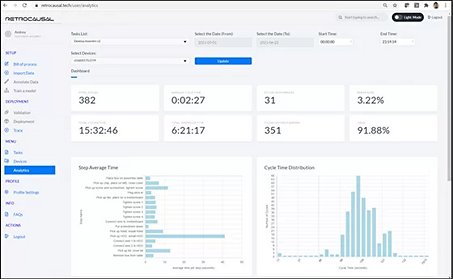
Another important point of the platform is the traceability of products for each assembly stage, extending the typical notion of Total Quality Management (TQM) to the entire manual production line.
This allows quality and industrial engineers to analyze the root cause of their computer problems, for example, and reduce product batches with recall events.
To find out how to have this cutting-edge technology for your manual assembly process, contact us.
Email: marketing.mae@macnica.com