Artificial intelligence in manual and repetitive assembly
When we talk about manual and repetitive assembly of products, we immediately think of Henry Ford and his changes to increase production efficiency, which are still recognized today. Among these changes was the restructuring of the production line, in which each employee carried out a part of the assembly and the equipment moved along a production conveyor belt.
This reduction in employee travel optimized activities. However, this division of manual and repetitive assembly activities is often not possible, and the employee needs to carry out the entire process at their bench. They need to master all the stages of the process.
Over time, the employee can become an expert in the activity. On the other hand, for companies facing high employee turnover, this can also be a problem. This is because, when the employee is gaining autonomy and doing their job well, they may change roles, generating a new training period for someone else to take on the task.
Artificial intelligence (AI) can help solve problems like these. Here's how AI can help optimize the training of new employees.
Artificial intelligence to help with manual and repetitive assembly
Employees who carry out manual and repetitive assembly of products or work at the packaging stage represent almost 80% of production work. Despite the increasing number of robots in industry, it is unlikely that the percentage of operators will decrease significantly due to the nature of the activities that are carried out in factories.
At the same time, it should be noted that 68% of quality problems are caused by human operators. In addition, there is a trend towards an increase in the number of temporary operators in factories. In the US manufacturing industry alone, the number of temporary workers has more than tripled in the last decade, and this is a category that is often poorly trained and motivated, generating quality problems in production.
Faced with this scenario, there are many production monitoring options on the market that help employees comply with standard work guidelines, such as:
- Internet of Things (IoT) solutions;
- projected augmented reality
- digital work instruction.
However, this reality is already changing, and many companies are already using Retrocausal's artificial intelligence solution, which, through technology, guides the employee in real time to minimize manual and repetitive assembly errors.
In the image below, you can see Retrocausal's system running and alerting the employee that a cable hasn't been connected properly. The alerts can even be made in a variety of ways, for example, by activating a lighting device, an audible alert, or a multimedia projector.
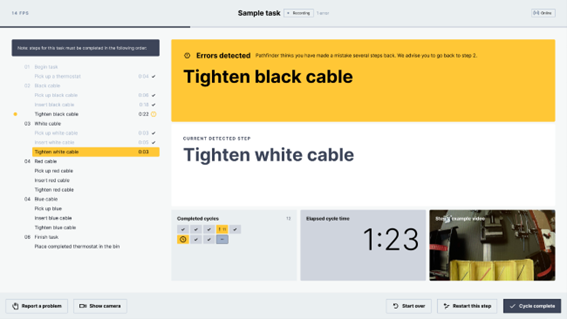
Retrocausal's AI solution for employee training
As we have said, artificial intelligence can make training new employees much easier and faster. And one of the options that can be used in these cases is Retrocausal's artificial intelligence solution, brought by Macnica ATD Europe to Europe. The solution's biggest differentiator is that it acts as an extra pair of eyes on the repetitive manual assembly line.
With a single camera, a computer and artificial intelligence, the Retrocausal solution enables constant monitoring and error detection in manual and repetitive assembly. In addition, it issues alerts immediately when it identifies possible faults, such as forgetting to tighten a screw or connect a cable, guaranteeing the precision and quality of production.

These types of errors, although common at the start of training a new employee or at the end of an exhausting working day, cause major damage, such as rework and even product loss. In addition to avoiding these problems, Retrocausal's artificial intelligence solution has an excellent cost-benefit ratio (ROI), as it speeds up training and guarantees a high level of quality for products that go through manual and repetitive assembly.
Do you want to speed up the training of your employees and increase the efficiency of your manual and repetitive assembly line? Contact us and schedule a meeting with our experts.