Movella Xsens - MTi Series
MTi Series
High Precision Module
MTi inertial measurement modules can provide accurate data, and the meaning of these data will be given according to your application. The following are examples of some common product applications.
Video:MTi applications
Autonomous Vehicles
In travel and transport, autonomous vehicles are on the rise. From autonomous trucks and self-racing cars, mobile robots and automated 3D surveying applications to train tracking technologies, the range of possibilities in this field is as extensive as the list of tech requirements is long. Xsens' solutions - which we present in our range of MTi-products can be used in any of these areas. With Controller Area Network (CAN) interface support as well as internal and external GNSS receivers, our solutions provide full inertial navigation and motion technology for indoor, outdoor and subterranean applications.
Marine and Ports
Maritime and port applications have to deal with many different factors, including highly changeable water and air motion. Reliability and precision are of the utmost importance in this field. Think for example, of underwater robotics, autonomous boats, maintaining the static stability of a ship on moving water, stabilized platforms for cameras or antennas, measuring sea or underwater motion, mapping the seafloor in hyperspectral detail, or maritime and port surveillance systems. The robust hard- and software, along with the anti-magnetic distortion filters of Xsens' MTi series, makes them a highly suitable, stable platform for motion technology applications at sea and in seaports.
Drones
Devices in this application area often have to be small and light-weight. Low latency is also important in drone applications: you want a system that is optimized to process high volumes of data with minimal delay. Another feature that matters to customers in this area is compatibility: with the range of GNSS receivers expanding all the time, you want an inertial sensor module that will easily slot into place. We support a wide range of customers in this field, many of them with our MTi-1 series. Weighing in less than one gram, the MTi-1 is the smallest Inertial Measurement Unit (IMU) on the market today.
Warehousing and Logistics
A major challenge in this area is that Global Positioning System (GPS) does not work inside most buildings, or underground. This means your drone or robotic arm has to operate reliably without the need for magnetic reference. It also means it must be self-aware and able to navigate an environment with objects that move, or are moved around. At the same time, price pressure is high in this fast-moving sector, with customers demanding excellent price-performance ratios, combined with high compatibility. Our Motion Tracking industrial-grade (MTi) products offer a variety of all-in-one solutions for these challenges. Especially the VRUs (Vertical Reference Units) are commonly used in this application area.
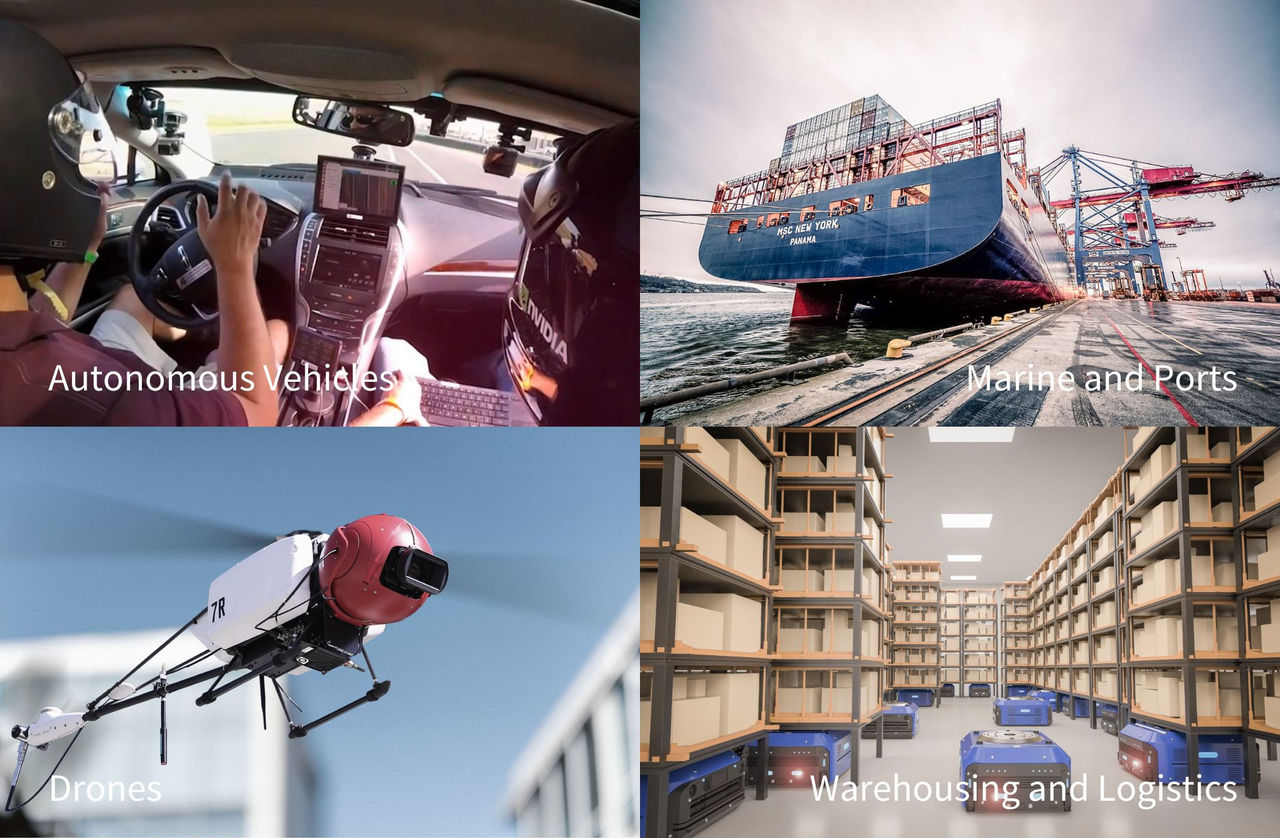
We enable solutions to a wide and constantly growing range of other industries and applications. In addition to those mentioned, these include:
Agriculture & forestry
Automotive-testing
Conducting & mining
Stabilization
Digital mapping & surveying
Product Introduction
Much of the inertial sensor modules available on the market today originated at Xsens, and it has close to 200 patents in the field. With Xsens you can rely on robust 3D (ego) motion data, even under difficult (magnetic) conditions – built on 20 years of continuous improvement of sensor fusion algorithms, software and component selection. Xsens products are tested in-house, factory-calibrated to numerous standards, and temperature bias-calibrated to withstand extreme conditions.
Xsens products are highly configurable with all the (data) synchronization options you need to integrate them in your unique industrial ecosystem. Xsens plug and play modules – the widest portfolio on today’s market – offer three different form factors with eight interface options, so you can confidently build on your own needs and specs. Save time and money, while enjoying maximum creative freedom in developing the perfect solution for your application.
Inertial Measurement Unit (IMU)
An Inertial Measurement Unit (IMU) is a self-contained system that provides raw, calibrated sensor data regarding linear and angular motion.
The quality of an IMU is partly defined by the sensing elements included in it. In a market in which sensor components or modules can range in price from 1 to 1,000 USD, many engineers give in to the temptation of using lower-end options – also to reduce the risk of over-performance.
In practice, however, preparing consumer-grade systems for real-world industrial application requires such extensive conditioning and processing that opting for an industrial-grade module is often more cost-effective – and a lot less stressful and time-consuming for the client.
In addition to component quality, the quality of your signal processing pipeline is important. Our IMUs are accurately calibrated, providing a model of the internal sensors. In operation, the signal processing chain consists of four links:
Sampling (at a high frequency)
A carefully designed digital low pass filtering in order to prevent aliasing
Application of the calibration model
Strapdown Integration (SDI) at the high frequency of 2 KHz
Xsens’s well-tested design of this entire signal processing pipeline ensures that your IMU will deliver high-fidelity data.
An IMU is your best choice when you need the following data:
3D acceleration
3D rate of turn
3D magnetic field
Vertical Reference Unit (VRU)
A vertical reference unit (VRU) measures roll, pitch, and (unreferenced) yaw. Its sensor-fused data – which can include the heading and other kinds of data, depending on the application and required performance level – is used for dynamic positioning in a variety of contexts. VRUs are the perfect solution for locations with high magnetic interference, as they do not rely on magnetic referencing.
Although unreferenced, the yaw data delivered by our VRUs are superior to those produced by systems using only gyroscope integration. This is because we have integrated advanced on-board sensor fusion.
An VRU is the best choice for you if you need the following data:
3D acceleration, 3D rate of turn, 3D magnetic field
Free acceleration (no gravity component)
Roll/pitch (inclination)
Yaw (relative/gyro-based)
Attitude and Heading Reference System (AHRS)
An Attitude and Heading Reference System, or AHRS, provides 3D orientation by integrating gyroscopes and fusing this data with accelerometer and magnetometer data.
The yaw output is referenced to True North: with sensor fusion, drift that arises from the integration of gyroscope data is compensated for by reference vectors, namely gravity, and the earth’s magnetic field. This results in a drift-free orientation. The raw sensor signals are combined and processed at a high frequency, up to 400 Hz, to produce a real-time stream of 3D orientation data (roll, pitch and yaw) from the sensor.
The yaw can be referenced or unreferenced, depending on the setting in which the device is used. In applications in which a North-referenced heading estimate is essential, our AHRS provides this by measuring the earth’s magnetic field using 3-axis magnetometers: in other words, the magnetic field measurements are used as a compass reading. If the local earth magnetic field is disturbed temporarily – which occurs frequently in many industrial settings, such as indoor or underground warehouses – the on-board filters will identify this disturbance, maintaining a stable, North-referenced yaw.
An AHRS is your best choice if you need the following data:
3D acceleration, 3D rate of turn, 3D magnetic field
Free acceleration (no gravity component)
Roll/pitch (inclination)
Yaw (relative/gyro-based) or Yaw (absolute/magnetic North-referenced)
Global Navigation Satellite System/Inertial Navigation (GNSS/INS)
A regular INS uses angular velocity and acceleration data from an IMU to compute a relative position over time. This means it will drift from its true position if no external reference is provided. A GNSS can provide this reference. The combination of mutually enhancing GNSS, INS and AHRS techniques enables us to provide you with powerful navigation solutions offering the best performance and the least amount of drift.
An GNSS/INS is your best choice if you are in need of the following data:
3D acceleration, 3D rate of turn, 3D magnetic field
Free acceleration (no gravity component)
Roll/pitch (inclination)
Yaw (relative/gyro-based) or Yaw (absolute/magnetic North-referenced)
Latitude, longitude, altitude
3D velocity
Real-Time Kinematic positioning (RTK GNSS/INS)
Real-Time Kinematic (RTK) positioning is a satellite navigation technology used to increase the precision of position data obtained from satellite positioning systems. RTK solves this issue by using real-time corrections from a base station. The base station knows its fixed position and therefore is able to estimate the errors of the received signals. This correction signal is then transmitted from the base station to the RTK receiver.
A RTK is your best choice if you are in need of the following data:
3D acceleration, 3D rate of turn, 3D magnetic field
Free acceleration (no gravity component)
Roll/pitch (inclination)
Yaw (relative/gyro-based) or Yaw (absolute/magnetic North-referenced)
Latitude, longitude, altitude
3D velocity
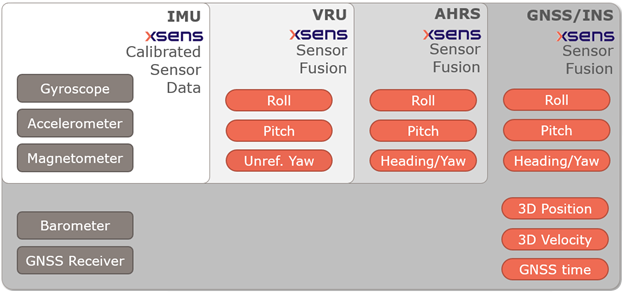
Product Series
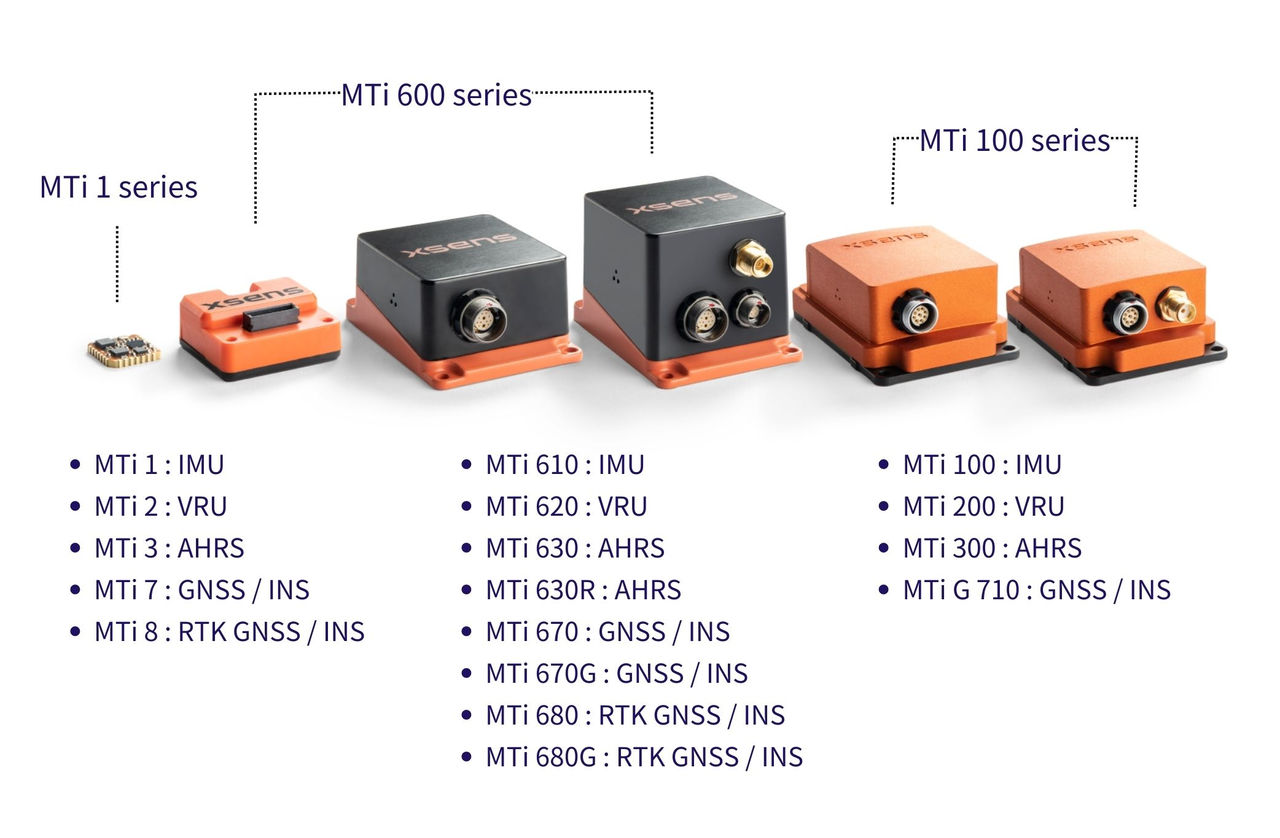
All products contain a 3D IMU composed of a gyroscope and an accelerometer plus a 3D magnetometer, with optionally a barometer and GNSS receiver. The MTi product range is divided into several series; the MTi 1-series, the MTi 600-series, the MTi 100-series.
MTi 1-series
The MTi 1-series is our entry-level solution. At just 12mm x 12mm, it offers the smallest form factor. MTi-1 is surface-mountable, and typically used for high-volume applications.
MTi 600-series
The MTi 600-series is the most versatile of our industrial-grade products, and your safest bet for almost any kind of industrial application. The newest lines offer refined sensor fusion algorithms, containing the most technologically cutting-edge components.
MTi 100-series
The MTi 100-series is Xsens’ highest performer. Ruggedly built, this all-in-one sensor system comes with the most advanced enhanced sensor fusion core, setting the industry standard for reliable MEMS-based INS, AHRS, VRU and IMU solutions.
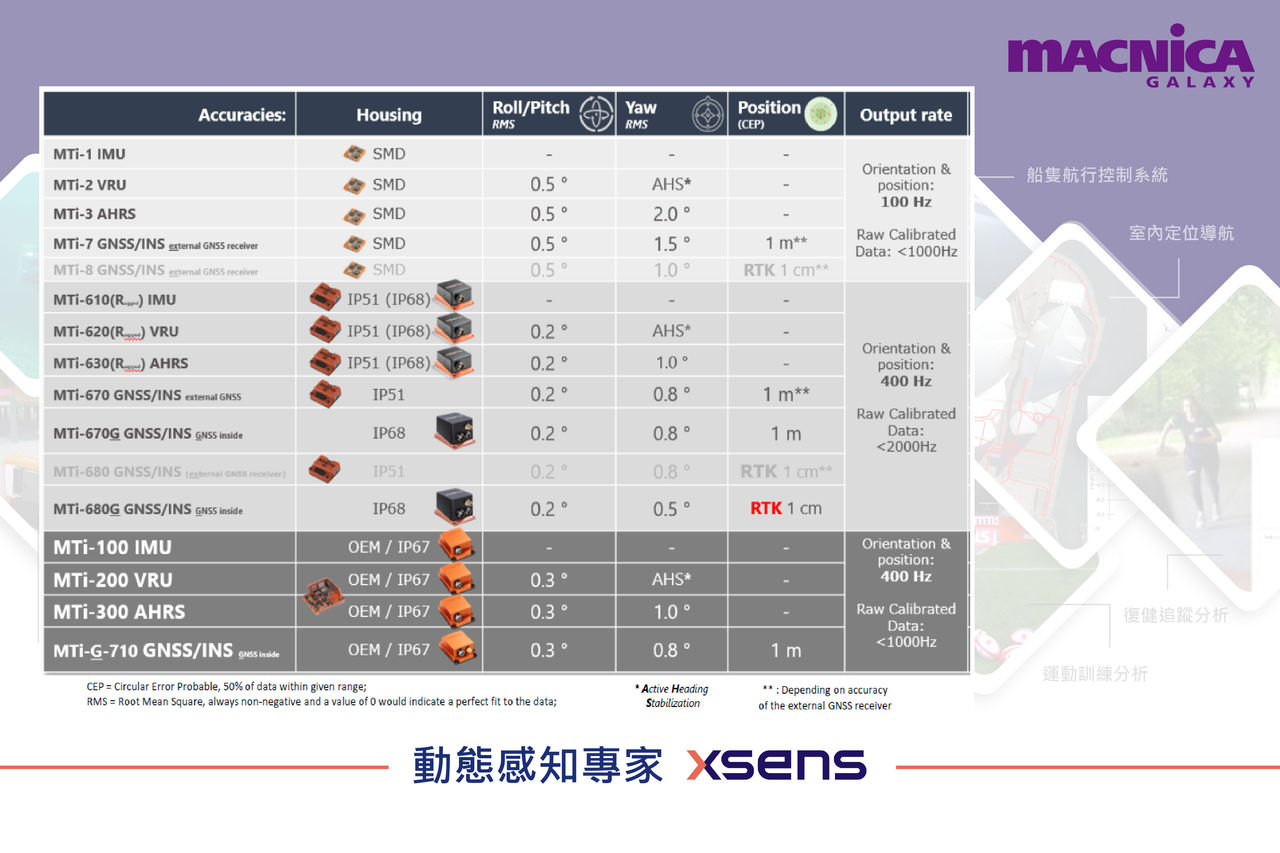
Welcome to contact Macnica Galaxy and we will assist you in selecting the right MTi module for your application.
Successful Case
Autonomous Service Robot
The room service robot from Germany-based Robotise - JEEVES®,The fully autonomous service robot, called JEEVES, is the world’s first to comply with the European Union’s safety regulations governing the operation of robots in public spaces.
Robotise selected the Movella MTi-610 series because its features are particularly well suited to fully autonomous operation on battery power. With a footprint of just 28mm x 31.5mm and weighing less than 10 grams, the unit provides JEEVES with highly accurate and reliable 3D motion tracking data.
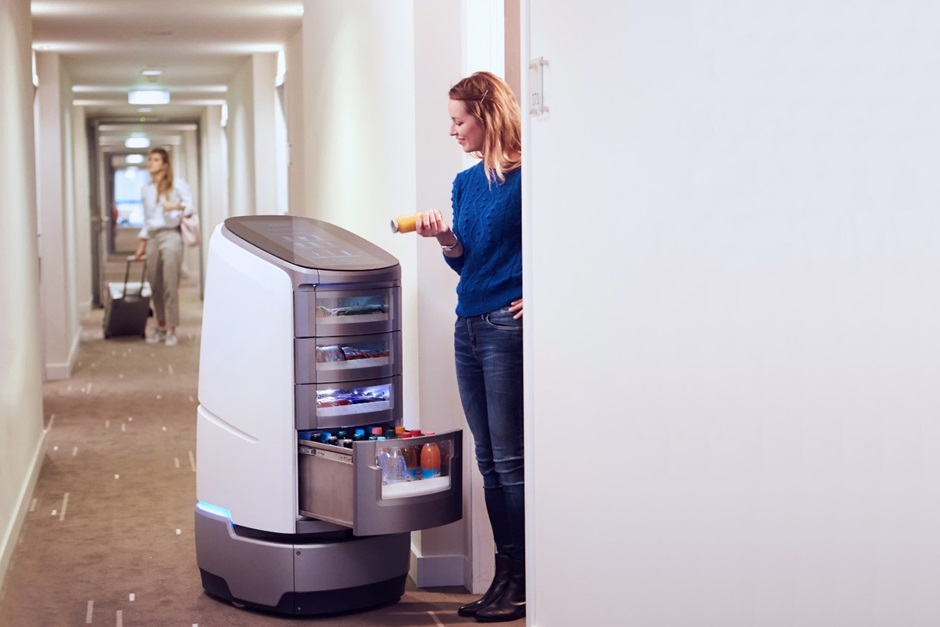
Wave Measurement Sensor
For decades wave measurement was a low-technology, expensive process which required the deployment of large, special-purpose buoys. Seaview Systems, based in Dexter, Michigan in the US, introduced a wholly new approach — SVS-603HR Wave Sensor, it is based on an MTi-3 motion sensor from Xsens. Buoys equipped with an SVS-603HR wave sensor are small, light, and easy to launch.
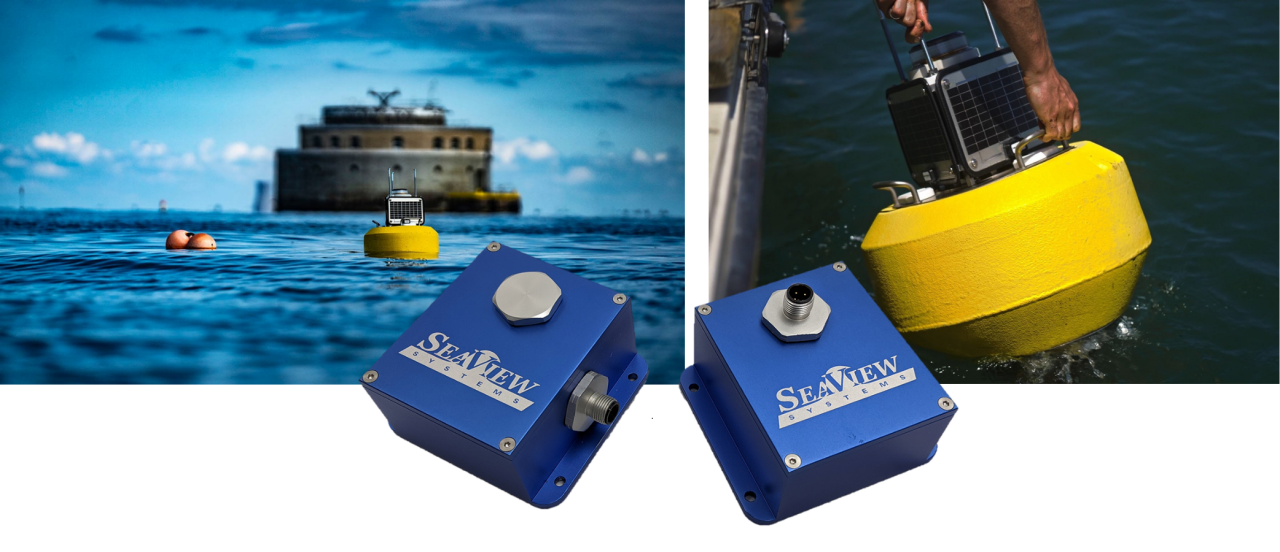